

How do you know your sanitation program is effective? How do you measure your success? What tools do you know about and use within your sanitation program? I like to say that cleaning and sanitation is a program, not a single tool. We don’t just use a screwdriver, we use the entire toolbox when we complete this program.
I thought in this column we could talk about many of the tools that are in our toolbox when we are working on cleaning and sanitation. I think many folks would be surprised to see that there are so many tools used. Let’s take a look in that toolbox.
Before we even start cleaning and sanitizing, we have tools to help us keep any contamination out of the room (or in the room in some cases!). We have automated hand and boot washers. These automated pieces of equipment standardize hand and footwear washing to minimize cross contact or contamination. Our goal is consistency and continuous improvement, so when we make these processes consistent, we improve the operation.
Pest Control. Most people think pest control is a program, and generally, it is. However, it is also a tool to keep the plant clean. Minimizing pests that wander around your facility prevents tracking pathogens into and around the facility. All those large and small pests carry pathogens and other ugly microorganisms that can easily contaminate your facility, ingredients and even your product handling equipment. Use this as a tool to make it easier to keep the facility clean. It is interesting to note that pest control is a tool in cleaning and sanitation, but cleaning and sanitation is also your No. 1 control for not inviting pests into your facility. There is a symbiotic relationship between these programs.
Cleaning Equipment and the Facility. To enable proper cleaning of each piece of equipment and the facility itself, there are new brush designs that are made just for certain equipment. Cleaning metal and other hard surfaces requires the use of certain types and designs of tools. Cleaning facility areas (walls and floors) should use a different type of tool design. Vikan offers its UST cleaning products with different bristle angles to clean different equipment, and the space between bristles enables better cleaning of the tools themselves. Perfex and Hillbrush use different textures and stiffness of bristles for cleaning different areas.
To prevent tools from being used in various areas of the facility or to clean only certain lines, use color-coded cleaning equipment. This is an appropriate tool for separating an allergen-containing product line and is used in facilities to separate production rooms (raw and treated food areas, for example). Providers offer seven to 12 different colors of cleaning equipment.
Ensuring that damaged cleaning materials can be found, Hillbrush also offers a metal detectable line of tools (unfortunately in only one color so far). Hillbrush also provides shadow boards that can help ensure the right tools are kept in the right place and are available when your team needs them.
When it comes to actually completing the cleaning and sanitation, we know that we don’t have all the experts on our staff, so we use contract providers for our cleaning chemical supply and for cleaning services.
These experts in cleaning technology help us to optimize our efforts. Making your cleaning and sanitation process consistent and improving your cleaning processes is the task of many chemical supplier representatives. Whether you’re using one of the major nationwide suppliers or a local provider, these companies have years of experience and can help you with all your issues. Cleaning a deep fat fryer is different from cleaning a conveyor belt or a piece of packaging equipment. All of that is completely different from clean-in-place systems.
There are providers available now that will clean using high-pressure steam, cold water and even carbon dioxide instead of chemicals and elbow grease. Which chemical to use, at what concentration, what to use it on and how to do it well are the purview of these contract providers. If you’re using one, make sure you’re getting the most out of them. If you’re not using one, think about adding this tool to your toolbox.

The Role of Testing. Measuring your success is made easier now with rapid microbial testing. Thirty years ago, we’d swab a cleaned and sanitized surface and then wait two to five days to confirm it was really clean. The modern technology of ATP swabbing has reduced that turnaround time to just a few minutes. Use ATP swabbing to assure that the lines, systems and equipment are clean prior to starting to use that equipment.
Rapid allergen swabs are also available for at least the major allergens. Use these to ensure allergen residues are removed from equipment prior to starting on a new product.
Your environmental monitoring program (EMP) is used to understand and manage pathogen movement within a plant and can be used to help measure your program success. After cleaning and sanitation, try to find pathogens in your plant. This is your measure of cleaning success and can be used to help you identify areas with a need for improvement.
Does your routine cleaning and sanitation program eliminate pathogens from your facility? This program is a verification of sanitation and a continuous improvement program for sanitation. Be sure to react appropriately when you do find pathogens in your plant to make this an especially effective program.
In many cases, it is difficult to find or identify pathogens using standard testing. Test for indicator organisms instead of the actual pathogen. Indicator organisms can certainly tell you if your cleaning and sanitation are effective. Instead of testing for E. coli 0157, test for generic E. coli or even STEC. Instead of testing for Listeria monocytogenes, test for Listeria species. Instead of testing for a specific organism, test for a generic class such as coliforms.
Much of the scientific work done has shown that finding that one strain (L. mono, for example) from a mixed culture is extremely difficult, and it’s unlikely you’ll find that one organism. Looking for the indicator still provides you with valuable information that you can use to improve your program.
One More Tool. Now that we’ve implemented programs and are using all these tools, we have one more to help us track results of product and production line swabs at pre-op. Electronic data collection fed directly into a quality management system (QMS) software program can help you predict where your next problem will be.
Use a QMS tool to track all the data you generate over time. The QMS programs are designed to help you recognize when things are starting to go bad so that you can implement corrective action before the problem results in product destruction or even a recall. There are many QMS programs available, so I won’t mention any. Just be sure that what you’re using is truly helping you to identify areas for improvement.
To summarize, be sure you’re using all the tools in your toolbox when it comes to cleaning and sanitation.
These tools complement and build on each other to make the entire cleaning and sanitation program effective. Using all the tools will surely make your operation more consistent and will help you find the areas for needed continuous improvement.
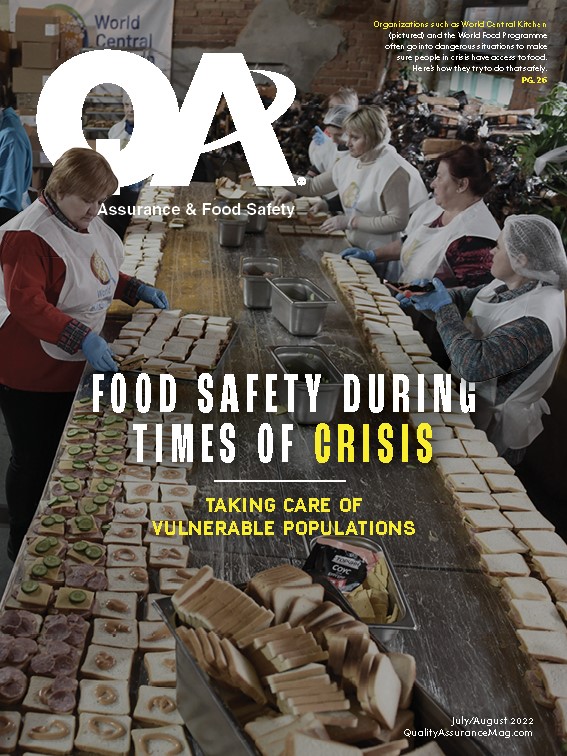
Explore the July August 2022 Issue
Check out more from this issue and find you next story to read.
Latest from Quality Assurance & Food Safety
- FDA Issues Update on Post-Market Assessment of Tara Flour
- ASI Announces Training Partnership with Rootwurks
- Nfinite Nanotech Closes $6.5 Million Seed Financing to Create Flexible Food Packaging with Nanotechnology
- University of Pretoria Food Science Student Wins IFT and PepsiCo’s Academic and Travel Undergraduate Hybrid Scholarship
- Kraft Natural Cheese and Shawn Johnson East Celebrate Launch of Kraft Signature Shreds
- Natural Sourcing International Announces Voluntary Recall of Black Chia Seeds
- PTNPA's DC Fly-In Connects Members with Policymakers
- Breck Partners Acquires NPX One